Tuesday, July 29, 2025
Masonite International - Manufacturing Production Trainer
Post-Hire Training
Recruitment #10-535-02
Company | Masonite International |
---|---|
Date Opened | 12/13/2021 12:00:00 PM |
Filing Deadline | 1/23/2022 11:59:00 PM |
Location | Fort Mill, SC |
Introduction
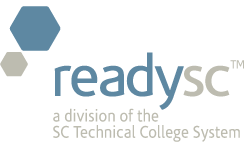
is assisting with the recruitment and training for

At Masonite we’ve spent over 95 years looking into the future, constantly developing ways to make our products safer, smarter, cleaner, more stylish and more functional. And because we push ourselves to do more, we’re able to deliver more. Masonite was built on a foundation of innovation, and that spirit of innovation continues to thrive today. Masonite is the leading manufacturer and distributor of interior and exterior doors, door components, and door entry systems.
Employment opportunities exist at our Fort Mill, SC manufacturing plant for:
Manufacturing Production Trainer
Overview:
The Manufacturing Production Trainer is responsible for leading and driving a consistent message about Masonite Production processes with an emphasis on creating and maintaining a safe working environment and maintaining and exceeding customer quality requirements. The Manufacturing Production Trainer will be expected to train, coach, and develop new team members, existing team members who move to new positions, improve skill-sets, identify best practices and optimize the use of lean manufacturing and individual development tools in order to meet safety, quality, and production needs.
Responsibilities:
• Train operators in quality requirements for each individual position.
• Train operators on SOP’s and JSA’s.
• Communicate to management progress of training of each operator.
• Provide all paperwork related to training.
• Cross-train employees based on 3x3 matrix requirements.
• Assist in the development of training documents and SOP’s.
• Schedule, coordinate and evaluate training activities.
• Coordinate with Managers, Supervisors, and Human Resources in order to assess training needs.
• Audit processes to ensure compliance.
• Maintain training records.
• Operate machinery required for particular position in a safe and efficient manner, to include training of new and existing operators in the carrying out of their duties.
• Inspect product for defects and take appropriate action as per SOP’s.
• Train employees to assemble product as per instructions with a focus on quality and safety.
• Practice and teach Masonite Lean Manufacturing Techniques including 5S+1.
• Train employees to communicate efficiently with other employees and the leadership team in order to ensure quality product is made timely.
• Train employees to read and interpret list counts and complete all departmental paperwork correctly and timely.
• Perform weekly EHS audits.
• Participate in Safety Kaizens and Haleyville Masonite Plant Kaizens. Help create/implement poke yokes for quality issues.
• Teach new and existing employees to read, understand, and follow production schedules
• Train employees to set up and adjust equipment.
• Perform minor preventative maintenance and operator care as required
• Assist Management, Maintenance and Quality personnel when troubleshooting equipment, process or material issues.
• Coach and train on the process and importance of maintaining downtime records and production information as appropriate.
• Perform housekeeping duties.
• Perform miscellaneous duties as assigned.
• Wear appropriate personal protective equipment.
• Work safely and follow safety rules and procedures.
Skills/Qualifications:
• Minimum of one (1) year experience in a training, mentoring, or leadership role.
• Understanding of all company policies, procedures, and safety requirements.
• Excellent written and oral communication skills.
• Basic math skills.
• Strong work ethic.
• Read interpret ticket.
• Basic reading and writing skills.
• Ability to add and subtract fractions and whole numbers, convert fractions to decimals
• Proficient at reading/interpreting, quality specs, proper door construction, door types, core types, stile/rail/block types.
• Excellent leadership and communication skills with the ability to give direction and lead others; ability to take action as necessary in line with company procedures and guidelines
• Good attendance and the ability to work flexible shifts and overtime as requested by management.
• Strong facilitation skills.
• Ability to multi-task & handle task with competing priorities.
• Proven analytical and problem solving skills.
• Ability to lift up to 80 lbs, bending, twisting, stooping, walking, must work at a fast pace and handle multiple parts that have glue on them.
• Strong eye/hand coordination.
• Ability to stand for long continuous hours.
• Ability to work in a mildly controlled environment - can expect some cold and heat during extreme weather conditions, with a significant amount of dust.
Apply HERE for the position.
You will be taken to another site to complete your application.
THIS JOB DESCRIPTION IS NOT AN EMPLOYMENT CONTRACT; Masonite is an "AT-WILL EMPLOYER"
An Equal Opportunity Employer