Friday, April 26, 2024
Masonite International - Team Leader
Post-Hire Training
Recruitment #10-535-03
Company | Masonite International |
---|---|
Date Opened | 12/13/2021 12:00:00 PM |
Filing Deadline | 1/23/2022 11:59:00 PM |
Location | Fort Mill, SC |
Introduction
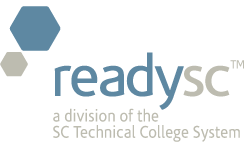
is assisting with the recruitment and training for

At Masonite we’ve spent over 95 years looking into the future, constantly developing ways to make our products safer, smarter, cleaner, more stylish and more functional. And because we push ourselves to do more, we’re able to deliver more. Masonite was built on a foundation of innovation, and that spirit of innovation continues to thrive today. Masonite is the leading manufacturer and distributor of interior and exterior doors, door components, and door entry systems.
Employment opportunities exist at our Fort Mill, SC manufacturing plant for:
Team Leader
Overview:
Reporting to the Production Supervisor, the Team Leader will be a proven leader and mentor. Qualities we look for are: problem solving skills, someone that promotes safe work environment, utilizes resources (HR, HSE, Quality, Purchasing), and can motivate while assisting in the assessment/understand/utilization of their department’s strengths and weaknesses.
You will assist the Production Supervisor in the overall production and delegation of work assignments to ensure all key performance indicators (KPIs) are identified, measured, and addressed. The Team Lead will need to have the ability to utilize production boards to keep employees enlightened and informed of the department performance against standards, working with them to correct deficiencies.
Part of your job will be to assist in the administration of plant rules and other policies and procedures in a fair and equitable manner. As a Team Lead, you will also be required to spend the majority of your time on the production floor. You will also be required to complete daily audits and constantly monitor employee and machine performance to optimize efficiency. The Team Lead will also be required to lead Tier 1 meetings, as well as participate in other Tier meetings with senior leadership using appropriate decision-making tools gaining approval before implementing decisions or changes.
Key Deliverables:
• Safety: enforce safety practices, tolerance to zero attitude, maintain safety engagement.
• Quality: understand the standards & requirements, work with precision and attention to details.
• Delivery: Just in time production strategy.
• Inventory: Manage and be aware the inventory levels in the production area.
• Productivity: measure the efficiency of the employees, equipment and overall cost efficiency.
• Build employees trust: By knowing when to be transparent and when to listen and when to follow up to settle employee concerns.
Qualifications:
• Minimum of one (1) year leadership experience in a team-based Lean Manufacturing environment.
• Computer literacy with proficiency in MS Office, Excel, Outlook, preferred.
• Hands-on experience managing Lean Manufacturing process systems.
• Excellent communication skills.
• Reliable with high integrity and strong work ethic.
• Self-motivated with a-results driven approach.
• Excellent problem-solving skills.
• Ability to work with little to no supervision if needed.
• Understanding of all company policies, procedures, and safety requirements.
• Basic math skills.
• Strong work ethic.
• Read interpret ticket.
• Basic reading and writing skills.
• Ability to add and subtract fractions and whole numbers, convert fractions to decimals
• Proficient at reading/interpreting, quality specs, proper door construction, door types, core types, stile/rail/block types.
• Excellent leadership and communication skills with the ability to give direction and lead others; ability to take action as necessary in line with company procedures and guidelines
• Good attendance and the ability to work flexible shifts and overtime as requested by management.
• Strong facilitation skills.
• Ability to multi-task & handle task with competing priorities.
• Proven analytical and problem-solving skills.
Physical Demands:
• The employee must have the ability to read and write and to use a computer.
• While performing the duties of this job, the employee is frequently required to stand.
• The employee is frequently required to perform repetitive motions.
• The employee frequently is required to walk, use hands to feel or handle, and to reach with hands and arms.
• Ability to lift up to 80 lbs, and is frequently required to bend, twist, stoop, walk, and ability to at a fast pace and handle multiple parts that have glue on them, and to stand throughout entirety of shift.
• The employee will be working in a facility that is not climate controlled; therefore, exposure to heat and/or cold is possible.
• The employee will be working in a facility with a high level of forklift traffic.
• Intense and high level of concentration to focus on product quality and productivity.
• Strong eye/hand coordination
• Ability to work in a mildly controlled environment - can expect some cold and heat during extreme weather conditions, with a significant amount of dust
• Good attendance and ability to work overtime and weekends when circumstances and workload requires, as assigned by management.
Apply HERE for the position.
You will be taken to another site to complete your application.
THIS JOB DESCRIPTION IS NOT AN EMPLOYMENT CONTRACT; Masonite is an "AT-WILL EMPLOYER"
An Equal Opportunity Employer